Thu hồi Kẽm Oxit từ xỉ thải của làng nghề Đại Bái (Gia Bình, Bắc Ninh) bằng phương pháp thủy luyện
Từ trước đến nay, lượng xỉ thải này chưa được các hộ gia đình hoặc các cơ quan, tổ chức quan tâm xử lý nhằm thu hồi kim loại có trong xỉ. Hầu hết lượng xỉ thải này được thu gom và vận chuyển bán ra bên ngoài dẫn đến sự ô nhiễm môi trường trong quá trình vận chuyển, lưu trữ xỉ.
Vì vậy, việc nghiên cứu thu hồi kim loại có trong xỉ sẽ làm giảm sự ô nhiễm môi trường, tận thu khoáng sản, gia tăng lợi nhuận cho quá trình sản xuất tại làng nghề.
2. Nội dung nghiên cứu
2.1. Mẫu nghiên cứu
Mẫu nghiên cứu là mẫu xỉ thải đặc trưng được lựa chọn và lấy mẫu tại làng nghề Đại Bái, huyện Gia Bình, tỉnh Bắc Ninh. Mẫu được lấy từ 30 hộ gia đình nấu, đúc đồng và có lượng xỉ thải lớn hơn 5 tấn/năm. Mẫu sau khi lấy về được trộn đều sau đó phân tích thành phần hóa học của xỉ, kết quả như bảng 1.
Bảng 1. Thành phần mẫu xỉ đồng
Thành phần | Zn | Cu | Fe | Mn | Ni | Al | Cr | Sn | Khác |
Hàm lượng, (%) | 30,27 | 6,60 | 2,43 | 0,17 | 0,05 | 6,36 | 0,06 | 0,14 | Còn lại |
Lượng xỉ thải của làng nghề Đại Bái hàng năm sinh ra >1.400 tấn, trong đó có ~400 tấn xỉ có chứa kẽm cần được thu hồi.
Đối với xỉ thải này có thể sử dụng phương pháp hỏa luyện hoặc thủy luyện để xử lý thu hồi kẽm. Tuy nhiện, đối với phương pháp hỏa luyện thường xử lý với khối lượng lớn (hàng chục nghìn tấn) do đó đối với xỉ thải chứa kẽm của làng nghề Đại Bái áp dụng phương pháp thủy luyện là phù hợp nhất.
Với đối tượng xỉ thải chứa kẽm, đồng, nhôm là chính, nhóm nghiên cứu đã sử dụng công nghệ thủy luyện bằng axit sunfuric đưa kẽm vào dung dịch, sau đó làm sạch các tạp chất, kết tủa kẽm cacbonat và nung để thu được kẽm oxit.
Các nội dung nghiên cứu chính như sau:
- Nghiên cứu quá trình hòa tách xỉ.
- Nghiên cứu quá trình làm sạch dung dịch.
- Nghiên cứu quá trình kết tủa kẽm cacbonat.
- Nghiên cứu nung thu hồi kẽm oxit.
3. Kết quả và thảo luận
3.1. Nghiên cứu hòa tách xỉ
Khối lượng mẫu dùng nghiên cứu cho mỗi thí nghiệm là 100g xỉ được hòa tách với axit sunfuric, tỉ lệ axit sunfuric thay đổi từ 30-50 ml/100g xỉ, nhiệt độ thay đổi từ 30-70oC, thời gian thay đổi từ 0,25 – 12h. Sau quá trình hòa tách lọc rửa bã sấy khô và phân tích hàm lượng kẽm trong bã để xác định hiệu suất hòa tách kẽm.
3.1.1 Nghiên cứu ảnh hưởng của nồng độ axit
Nồng độ axit được thay đổi từ 30, 35, 40, 45, 50 ml/100g xỉ, tương ứng với tỉ lệ 106; 123; 140; 157; 174 % so với lượng axit tính toán lý thuyết. Kết quả thể hiện trên Hình 1.
![]() |
Hình 1. Ảnh hưởng của tỉ lệ axit đến hiệu suất hòa tách. |
Kết quả cho thấy nồng độ axit ban đầu khi tiến hành hòa tách xỉ đồng thau có ảnh hưởng lớn tới hiệu suất hòa tách kẽm. Cụ thể, khi tăng nồng độ axit thì hiệu suất hòa tách của kẽm tăng. Trong đó, với lượng axit H2SO4 98% sử dụng dưới 35ml tương ứng lượng dư đến 123% so với tính toán lý thuyết thì hiệu suất hòa tách kẽm vẫn chưa cao. Nguyên nhân là do trong quá trình hòa tách có nhiều kim loại khác cùng hòa tan điển hình như sắt, nhôm, đồng, ... các nguyên tố này cùng phản ứng với axit do đó làm giảm đi hiệu suất hòa tách kẽm.
Khi tăng nồng độ axit, bắt đầu từ tỉ lệ 40 ml axit/100 g xỉ cho thấy hiệu suất hòa tách kẽm đạt 92,33 %, ở các tỉ lệ axit cao hơn như 45 hay 50 ml/100g xỉ hiệu suất hòa tách kẽm có tăng nhưng không đáng kể. Như vậy, để quá trình hòa tách đạt hiệu quả tốt đồng thời tránh dư nhiều axit gây phức tạp cho công đoạn tiếp theo thì tỉ lệ axit thích hợp nhất được lựa chọn là 40 ml axit H2SO4 98% để hòa tách 100g xỉ.
3.1.2 Nghiên cứu ảnh hưởng của nhiệt độ và thời gian đến quá trình hòa tách
Nhiệt độ và thời gian là hai yếu tố liên quan đến nhau quyết định hiệu suất quá trình hòa tách. Nhiệt độ cao giúp gia tăng tốc độ phản ứng từ đó có thể rút ngắn thời gian hòa tách.
- Nhiệt độ hòa tách gồm: không ổn nhiệt (nhiệt độ phòng ~30oC); ổn nhiệt ở 50oC; ổn nhiệt ở 70oC.
- Thời gian hòa tách: Ở mỗi nhiệt độ khác nhau, thời gian hòa tách được khảo sát ở 0,25; 4; 8; 12 (giờ).
Kết quả khảo sát ảnh hưởng của thời gian hòa tách với các nhiệt độ khác nhau được tổng hợp trên Hình 2.
![]() |
Hình 2. Ảnh hưởng của nhiệt độ và thời gian đến hiệu suất hòa tách kẽm |
Kết quả khảo sát quá trình hòa tách ở các nhiệt độ và thời gian khác nhau cho thấy hiệu suất hòa tách kẽm tăng theo chiều tăng của nhiệt độ và thời gian hòa tách.
Với thời gian chỉ 15 phút từ khi bắt đầu quá trình hòa tách thì hiệu suất hòa tách kẽm đã đạt >90%. Thời gian hòa tách là 4h ở nhiệt độ 70oC thì hiệu suất hòa tách kẽm đạt 93,36%; thời gian hòa tách là 12h ở nhiệt độ phòng thì hiệu suất hòa tách kẽm đạt 92,33%. Do đó để cân đối trong quá trình xử lý xỉ thu hồi kim loại, lựa chọn thời gian hòa tách là 4h ở nhiệt độ 70oC để thu kẽm từ xỉ đồng.
Tổng hợp chế độ hòa tách xỉ đồng thau đã xác định được như sau:
- Tỉ lệ axit H2SO4 98%: 40ml/100g xỉ.
- Ti lệ R/L: 1/5.
- Nhiệt độ hòa tách: 70oC.
- Thời gian hòa tách: 4 giờ.
3.2 Nghiên cứu làm sạch dung dịch kẽm sunfat
Trong dung dịch sau hòa tách có nhiều tạp như nhôm, sắt, đồng, v.v… Để thu được kẽm oxit sạch cần loại bỏ các chất tạp này ra khỏi dung dịch. Đối với nhôm rất dễ bị thủy phân vì vậy chỉ cần tiến hành điều chỉnh pH = 3 bằng bột kẽm sau đó lắng lọc dung dịch để loại bỏ phần lớn kết tủa nhôm ra khỏi dung dịch, phần nhôm còn lại sẽ tiếp tục được thủy phân cùng với quá trình khử sắt trong dung dịch.
Dung dịch thu được sau hòa tách có các thành phần như Bảng 2:
Thành phần | Zn | Cu | Fe | Al | Mn |
Nồng độ (g/l) | 50,65 | 11,83 | 4,20 | 3,63 | 0,25 |
3.2.1. Khảo sát các điều kiện, chế độ khử sắt trong dung dịch
Để khử sắt trong dung dịch cần oxi hóa sắt II thành sắt III và thủy phân tách ra khỏi dung dịch. Trong nghiên cứu này khảo sát ảnh hưởng của chất oxi hóa là H2O2 tới hiệu suất khử sắt, chế độ thí nghiệm như sau:
- pH khử sắt: 4,0.
- Lượng H2O2 50% sử dụng: 2; 3; 4; 5 (ml).
Kết quả ảnh hưởng của lượng H2O2 đến hiệu suất khử sắt được trình bày trong Hình 3:
![]() |
Ảnh hưởng cảu H2O2 tới quá trình khử sắt trong dung dịch |
Kết quả cho thấy hiệu suất khử sắt tăng khi tăng tỉ lệ H2O2 với tỉ lệ H2O2 là 4ml/1.000 ml dung dịch kẽm, hiệu suất khử sắt đạt 97,1%. Do đó, lựa chọn tỉ lệ chất khử H2O2 là 4ml/1.000 ml dung dịch để khử sắt.
3.2.2 Nghiên cứu tách đồng
Dung dịch sau khi đã khử tạp chất chứa đồng với nồng độ 11,53 g/l ở pH = 4,0. Khi nâng pH, Cu2+ trong dung dịch sẽ kết tủa trước dưới dạng đồng hydroxit bắt đầu từ pH ~ 4. Trong khi đó, Zn2+ bắt đầu kết tủa ở pH khoảng 6,5. Dựa vào đặc điểm này có thể tách phần lớn đồng ra khỏi dung dịch kẽm bằng cách thay đổi độ pH.
a. Ảnh hưởng của pH đến hiệu suất kết tủa đồng
Khảo sát pH tách kết tủa đồng thay đổi từ: 4,5; 5,0; 5,5; 6; 6,5. Trong quá trình kết tủa, dung dịch NaOH 10% được cấp đều vào dung dịch kết hợp với khuấy trộn để điều chỉnh pH. Khi pH dung dịch đạt tới giá trị khảo sát thì dừng cấp thêm NaOH sau đó lọc để tách dung dịch và kết tủa đồng hydroxit. Kết quả ảnh hưởng của pH tới quá trình kết tủa đồng được trình bày trong Bảng 3:
pH kết thúc kết tủa đồng | 4,5 | 5,0 | 5,5 | 6,0 | 6,5 |
Hiệu suất kết tủa đồng (%) | 15,3 | 78,2 | 92,6 | 94,5 | 97,1 |
Bảng 3: Ảnh hưởng của pH tới quá trình kết tủa đồng
Kết quả Bảng 3 cho thấy khi kết tủa đồng từ dung dịch bằng NaOH thì ở pH khoảng 4,5 đồng đã bắt đầu kết tủa. Trong khoảng pH từ 4,5 đến 5,5, lượng đồng kết tủa tăng nhanh theo lượng NaOH đưa vào. Cuối giai đoạn này, ở pH =5,5 đã có 92,6% đồng trong dung dịch kết tủa dưới dạng đồng hydroxit. Kể từ lúc này, NaOH đưa vào làm tăng pH trong khi lượng đồng kết tủa tăng không đáng kể. Hiệu suất kết tủa đồng ở pH = 6,0 là 94,5% và ở pH = 6,5 là 97,1%. Mặt khác từ pH = 5,5 bắt đầu có hiện tượng kẽm cũng bị kết tủa cục bộ, như vậy để kết tủa đồng hydroxit tương đối sạch kẽm và hiệu suất thu hồi kẽm cao thì chọn kết thúc quá trình kết tủa tách đồng ở pH < 5,5.
b. Ảnh hưởng của thời gian kết tủa đến hiệu suất tách đồng
Thời gian kết tủa đồng từ dung dịch được nghiên cứu thay đổi từ: 5; 10; 15; 20; 25 phút.
Thời gian kết tủa khảo sát là thời gian tính từ khi đưa dung dịch NaOH vào cho đến khi đạt đến pH kết thúc quá trình kết tủa hay nói cách khác là tốc độ đưa NaOH vào dung dịch. Kết quả khảo sát ảnh hưởng của thời gian đến quá trình kết tủa tách đồng khỏi dung dịch kẽm sunfat được trình bày trong Bảng 4:
Thời gian kết tủa đồng (phút) | 5 | 10 | 15 | 20 | 25 |
Hiệu suất kết tủa đồng (%) | 82,5 | 90,1 | 92,6 | 92,8 | 92,9 |
Bảng 4: Ảnh hưởng của thời gian tới quá trình kết tủa đồng
Kết quả cho ta thấy thời gian kết tủa hay nói cách khác là tốc độ đưa NaOH vào dung dịch không có ảnh hưởng nhiều tới hiệu suất kết tủa đồng. Tuy nhiên NaOH có tính kiềm mạnh và phản ứng rất nhanh với các ion Cu2+; Zn2+ trong dung dịch nên thường gây ra hiện tượng kết tủa cục bộ.
Khi tốc độ đưa NaOH vào dung dịch quá nhanh thì kẽm cũng bị kết tủa cục bộ và các hạt hydroxit kẽm tạo thành không có đủ thời gian để hòa tan trở lại do đó sẽ di vào bã kết tủa đồng. Mặt khác khi tốc độ đưa NaOH vào đủ chậm thì kẽm kết tủa cục bộ có thời gian để hòa tan trở lại nên kẽm ít bị kết tủa hơn. Từ kết quả khảo sát có thể thấy thời gian kết tủa đồng lựa chọn là 15 phút.
3.2.3 Nghiên cứu khử sâu các tạp chất còn lại trong dung dịch
Trong dung dịch kẽm sunfat sau khi tách phần lớn đồng dưới dạng hydroxit vẫn còn chứa một lượng nhỏ đồng. Cụ thể khi phân tích thành phần dung dịch sau khi tách đồng được kết quả như trong Bảng 5:
Thành phần | Zn | Cu | Fe | Al | Mn |
Nồng độ (g/l) | 70,82 | 0,86 | 0,06 | 0,03 | 0,005 |
Lượng đồng còn lại trong dung dịch là 0,86 g/l, khi kết tủa kẽm sẽ làm kẽm oxit bị đen. Do đó để thu được kẽm cacbonat sạch ta phải phải khử sâu hơn nữa đồng trong dung dịch. Với hàm lượng đồng còn lại trong dung dịch nhỏ, phương pháp khử hiệu quả là xi măng hóa bằng bột kẽm kim loại.
Đã tiến hành thử khử đồng bằng bột kẽm kim loại ở nhiệt độ 60oC, thời gian khử 2h, lượng bột kẽm kim loại là 5g/1.000 ml dung dịch.
Sau khử đem lọc để tách bã rắn không tan là hỗn hợp bột kẽm dư và các hạt đồng bị xi măng hóa. Dung dịch sạch thu được phân tích hàm lượng đồng, kẽm và một số tạp chất. Kết quả thu được như Bảng 6:
Thành phần | Zn | Cu | Fe | Al | Mn | pH |
Nồng độ (g/l) | 71,25 | 0,08 | 0,03 | 0,02 | 0,005 | 6,3 |
Bảng 6: Thành phần dung dịch sau xi măng hóa bằng bột kem
Hiệu suất khử đồng trong giai đoạn này là 90,7%. Các tạp chất còn lại trong dung dịch là nhỏ từ đó sẽ đảm bảo thu được kẽm cacbonat sạch ở công đoạn sau.
3.3. Kết tủa kẽm cacbonat
3.3.1 Ảnh hưởng của pH đến quá trình kết tủa kẽm cacbonat
Dung dịch kẽm sunfat sạch được kết tủa với tác nhân là Na2CO3. Để thực hiện kết tủa, cho dần dần dung dịch Na2CO3 bão hòa vào dung dịch kẽm sunfat và khuấy đều. Khảo sát ảnh hưởng của pH từ 7; 7,5; 8; 8,5; 9 tới hiệu suất kết tủa kẽm, thời gian kết tủa 15 phút.
Sau khi lọc lấy kết tủa, rửa và sấy khô, cân khối lượng kết tủa thu được và tính hiệu suất kết tủa kẽm. Kết quả được trình bày trong Bảng 7.
pH kết thúc kết tủa kẽm | 7,0 | 7,5 | 8,0 | 8,5 | 9,0 |
Hiệu suất kết tủa kẽm HktZn (%) | 70,6 | 92,3 | 98,5 | 99,8 | 99,9 |
Bảng 7: Ảnh hưởng của pH tới hiệu suất kết tủa kẽm.
Kết quả thực nghiệm cho thấy, ZnCO3 bắt đầu kết tủa mạnh từ pH = 6,5. Trong giai đoạn đầu của quá trình kết tủa, pH giữ gần như không đổi, do đó lượng ZnCO3 tạo thành tỉ lệ tuyến tính với lượng Na2CO3 đưa vào. Sau giai đoạn này, pH tăng rất nhanh, kể từ pH ~ 8 mặc dù tốc độ bổ sung Na2CO3 là không đổi so với giai đoạn trước. Hiệu suất kết tủa kẽm đạt khá cao ở khoảng pH ~8 chứng tỏ ở pH này kẽm trong dung dịch đã gần hết. Càng ở pH cao hơn kẽm kết tủa càng triệt để. Ở pH = 8,5 hiệu suất kết tủa kẽm đã đạt 99,8% là thích hợp để kết thúc quá trình kết tủa.
3.3.2. Ảnh hưởng thời gian đến quá trình kết tủa kẽm cacbonat
Thời gian kết tủa tương ứng với tốc độ đưa Na2CO3 vào dung dịch kẽm. Thời gian kết tủa được khảo sát từ 5, 10, 15, 20 phút; pH kết tủa là 8,5.
Kết thúc quá trình kết tủa, lọc để tách kẽm cabonat và phân tích hàm lượng kẽm còn lại trong dung dịch từ đó tính toán hiệu suất kết tủa kẽm. Kết quả khảo sát các thời gian kết tủa khác nhau được trình bày trong Bảng 8.
Thời gian kết tủa (phút) | 5 | 10 | 15 | 20 |
Hiệu suất kết tủa kẽm HktZn (%) | 86,5 | 95,9 | 99,8 | 99,8 |
Kết quả cho thấy: Với cùng một lượng Na2CO3 dùng để kết tủa kẽm nhưng khi tốc độ đưa Na2CO3 khác nhau thì hiệu suất kết tủa đạt được là khác nhau. Nếu thực hiện kết tủa trong thời gian ngắn (5 phút) thì hiệu suất kết tủa chỉ đạt được là 86,5%. Tăng dần thời gian kết tủa thì hiệu suất kết tủa tăng theo. Hiệu suất kết tủa đạt lớn nhất là 99,8% khi thời gian kết tủa là từ 15 phút trở lên. Tăng thời gian kết tủa tức là giảm tốc độ đưa Na2CO3 vào dung dịch hoặc phun dung dịch Na2CO3 trực tiếp lên bề mặt dung dịch kẽm kết hợp với khuấy trộn mạnh là các biện pháp có thể hạn chế hiện tượng kết tủa cục bộ.
Thời gian kết tủa cũng còn phụ thuộc vào lượng dung dịch kẽm. Qua khảo sát có thể đi đến kết luận ở quy mô xử lý 1 lít dung dịch thì thời gian kết tủa 15 phút là phù hợp.
3.4 Nung thu hồi kẽm oxit
3.4.1 Ảnh hưởng của nhiệt độ nung
Chế độ khảo sát ảnh hưởng của nhiệt độ nung như sau: Khối lượng mẫu kẽm cabonat đã sấy khô 200 g; thời gian nung 60 phút; nhiệt độ khảo sát: 150; 250; 350; 450; 550oC. Kết quả được trình bày trong Bảng 9.
Nhiệt độ nung (oC) | 150 | 250 | 350 | 450 | 550 |
Tỉ lệ giảm khối lượng thực tế Δmtt (%) | 4,8 | 28,6 | 32,6 | 32,7 | 32,7 |
Kết quả cho thấy, kết tủa kẽm cacbonat bắt đầu phân hủy mạnh ở nhiệt độ 250oC và sự phân hủy kẽm cacbonat thành ZnO cơ bản hoàn thành ở nhiệt độ khoảng 350oC. Tuy nhiên, ZnO không có chuyển biến thù hình khi nung ở nhiệt độ cao nên thực tế có thể tăng nhiệt độ nung lên 400oC để đảm bảo kẽm cacbonat được phân hủy hoàn toàn.
3.4.2 Nghiên cứu ảnh hưởng của thời gian nung
Để tối ưu chế độ nung phân hủy kẽm cacbonat, ngoài nhiệt độ nung đã được khảo sát ở trên cần lựa chọn thời gian nung phù hợp. Khảo sát ảnh hưởng của thời gian nung lựa chọn chế độ như sau:
- Khối lượng mẫu khô kẽm cabonat: 200 g.
- Nhiệt độ nung: 400oC.
- Tốc độ nâng nhiệt 10oC/ phút
- Thời gian nung: 15, 30, 45, 60, 75 phút.
Kết quả các thí nghiệm khảo sát ảnh hưởng của thời gian nung được trình bày trong Bảng 10.
Thời gian nung (phút) | 15 | 30 | 45 | 60 | 75 |
Tỉ lệ giảm khối lượng thực tế Δmtt (%) | 18,3 | 25,9 | 30,5 | 32,7 | 32,8 |
Kết quả cho thấy, độ giảm khối lượng của mẫu kết tủa kẽm cacbonat tăng dần theo thời gian nung. Điều này chứng tỏ thời gian nung càng dài thì lượng kẽm cacbonat chuyển biến thành ZnO càng cao. Với thời gian nung 60 phút ở nhiệt độ 400oC là đủ để phân hủy triệt để kẽm cacbonat thành ZnO, từ đó ta xác định được thời gian nung là 60 phút. Với chế độ này, kẽm oxit thu được đạt chất lượng 96,47% ZnO.
4. Kết luận
Bằng phương pháp thủy luyện kết hợp nung phân hủy đã thu hồi được kẽm oxit đạt chất lượng 96,47% ZnO.
Đây là các kết quả nghiên cứu sơ bộ và cho kết quả khá tốt, có triển vọng để áp dụng thu hồi kẽm oxit sạch từ xỉ đồng thau của các làng nghề tại Việt Nam. Đây là hướng nghiên cứu mới, có thể triển khai ở quy mô nhỏ khả năng ứng dụng cao, có thể áp dụng tại các làng nghề của Việt Nam.
ThS. Nguyễn Hồng Quân; ThS. Nguyễn Thị Lài
Viện Khoa học và Công nghệ Mỏ - Luyện kim
Tin mới
Tin khác
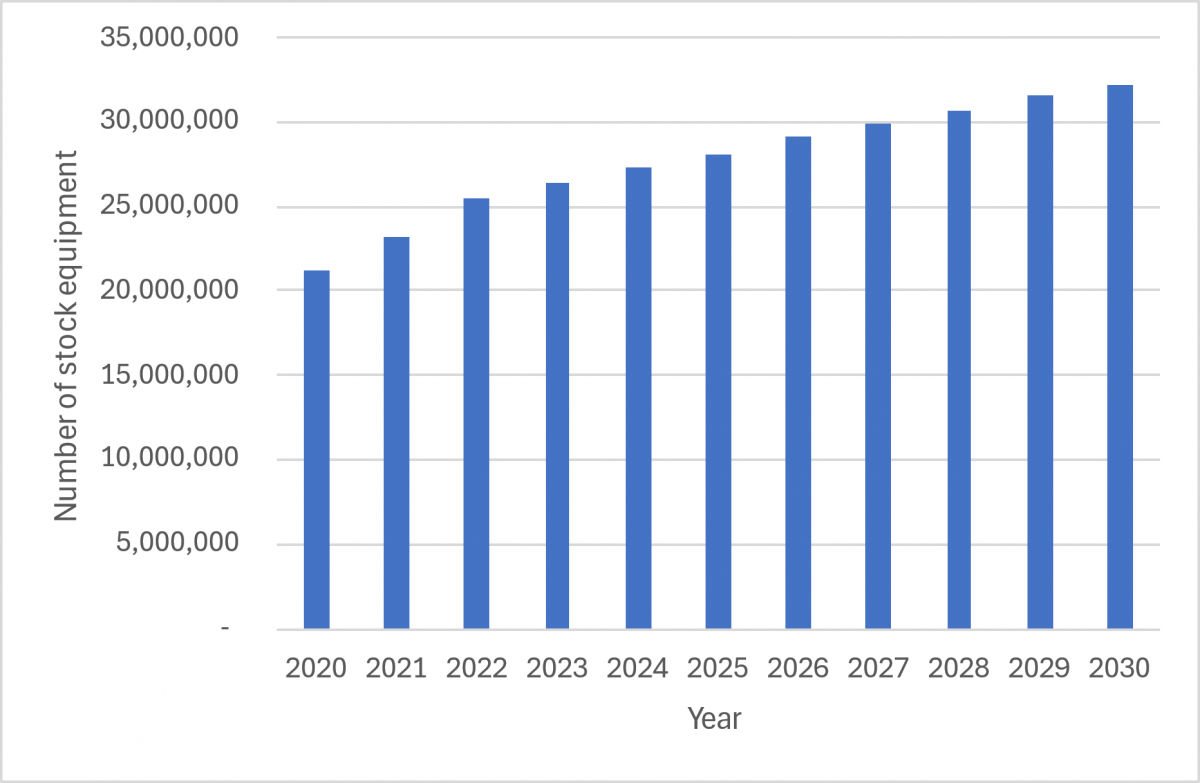
Kế hoạch chuyển đổi công nghệ lạnh xanh và môi chất lạnh tự nhiên đối với phân ngành lạnh gia dụng và bán lẻ trong chuỗi lạnh thực phẩm tại Việt Nam

Nghiên cứu thị trường và tình hình sử dụng thiết bị và môi chất lạnh của phân ngành lạnh gia dụng và bán lẻ trong chuỗi lạnh thực phẩm tại Việt Nam
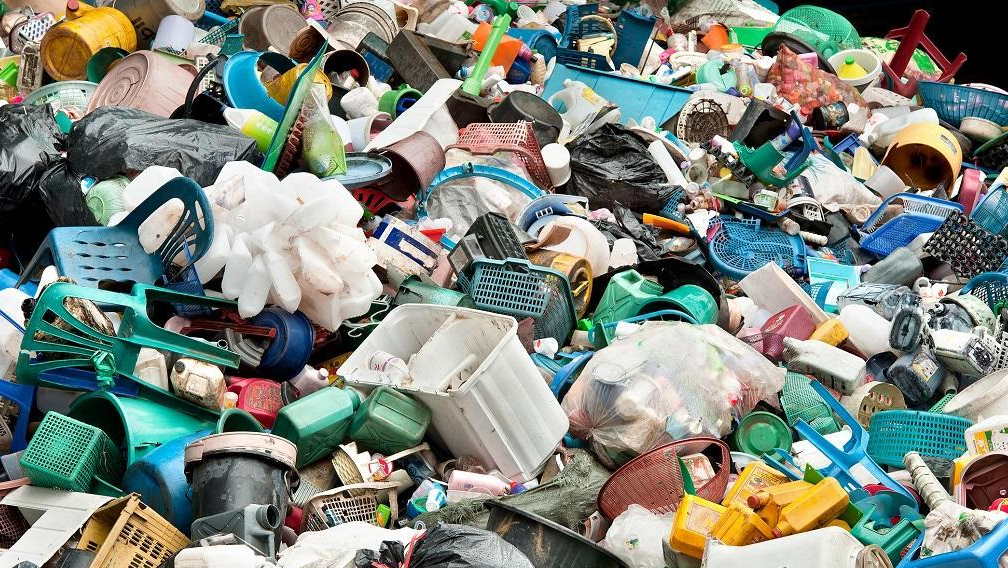